Destylacja rozpuszczalników to proces, który polega na oddzieleniu składników mieszaniny na podstawie różnicy ich temperatur wrzenia. W praktyce oznacza to, że rozpuszczalnik, który ma niższą temperaturę wrzenia, odparowuje jako pierwszy, a następnie skrapla się i zbiera w osobnym naczyniu. Kluczowym elementem tego procesu jest zastosowanie odpowiedniego sprzętu, takiego jak kolumna destylacyjna, która zwiększa efektywność separacji poprzez wielokrotne skraplanie i odparowywanie. Warto zaznaczyć, że destylacja jest szczególnie skuteczna w przypadku substancji o znacznie różniących się temperaturach wrzenia. Proces ten znajduje szerokie zastosowanie w przemyśle chemicznym oraz farmaceutycznym, gdzie czystość rozpuszczalników ma kluczowe znaczenie dla jakości finalnych produktów. Ponadto, destylacja może być stosowana do odzyskiwania rozpuszczalników z odpadów przemysłowych, co przyczynia się do ochrony środowiska i oszczędności surowców.
Jakie są zastosowania destylacji rozpuszczalników w przemyśle
Destylacja rozpuszczalników znajduje szerokie zastosowanie w różnych gałęziach przemysłu, co czyni ją jednym z kluczowych procesów technologicznych. W przemyśle chemicznym jest wykorzystywana do oczyszczania surowców oraz produkcji wysokiej jakości substancji chemicznych. Na przykład, w produkcji alkoholi etylowych destylacja pozwala na uzyskanie czystego produktu poprzez usunięcie niepożądanych zanieczyszczeń. W przemyśle farmaceutycznym proces ten jest niezbędny do uzyskania czystych rozpuszczalników wykorzystywanych w syntezach leków oraz ich formulacjach. Również w branży kosmetycznej destylacja jest stosowana do pozyskiwania esencji zapachowych oraz olejków eterycznych z roślin. Dodatkowo, w przemyśle petrochemicznym destylacja frakcyjna jest kluczowym etapem w rafinacji ropy naftowej, gdzie różne frakcje są oddzielane na podstawie ich temperatur wrzenia. Dzięki temu możliwe jest uzyskanie paliw oraz innych produktów chemicznych o określonych właściwościach.
Jakie są różnice między metodami destylacji rozpuszczalników
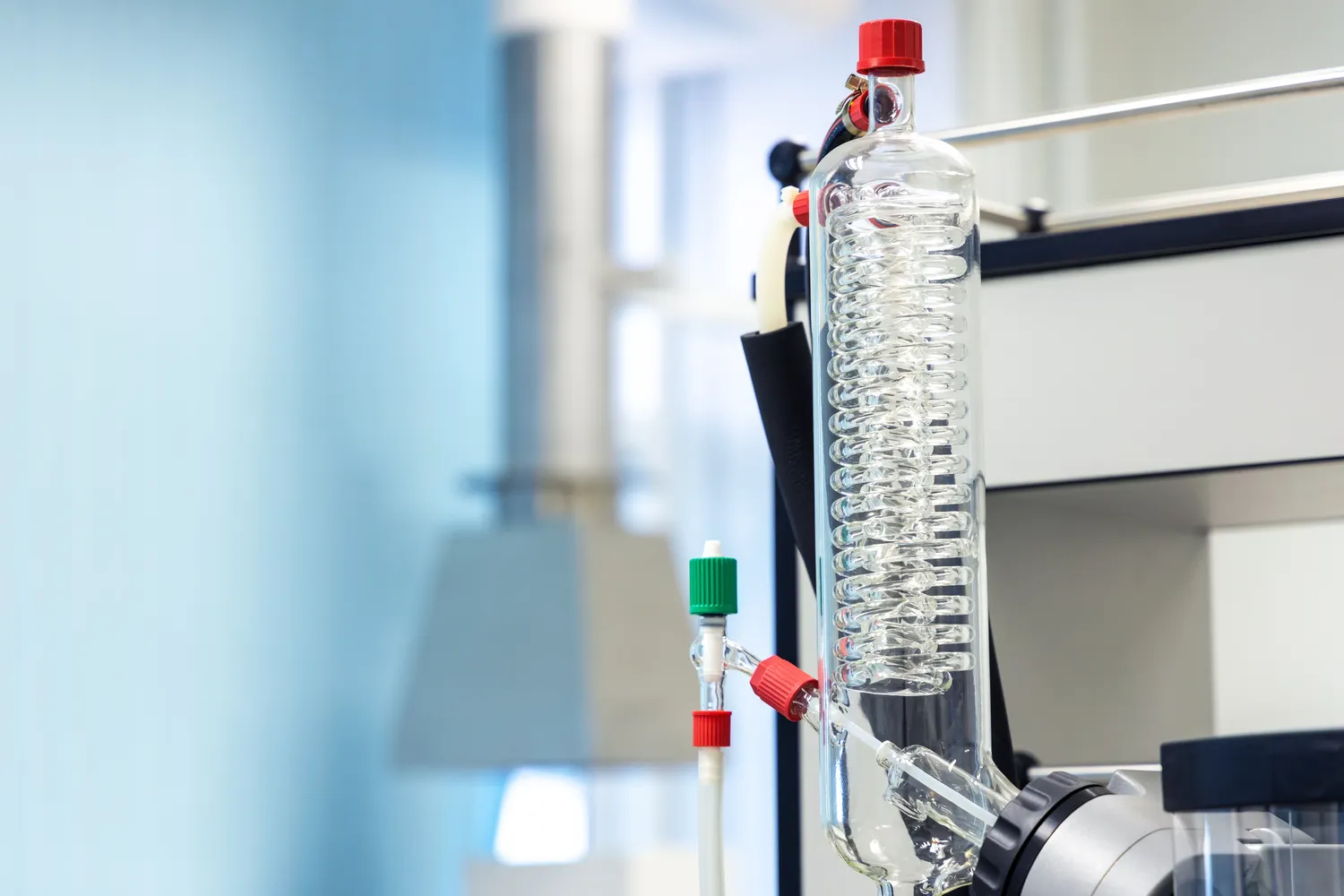
W kontekście destylacji rozpuszczalników istnieje kilka metod, które różnią się między sobą zarówno zasadą działania, jak i zastosowaniem. Destylacja prosta jest najprostszą formą tego procesu i polega na jednorazowym podgrzewaniu mieszaniny oraz zbieraniu pary. Jest ona skuteczna tylko wtedy, gdy składniki mają znacznie różniące się temperatury wrzenia. Z kolei destylacja frakcyjna wykorzystuje kolumnę destylacyjną do wielokrotnego skraplania i odparowywania składników mieszaniny, co pozwala na uzyskanie wyższej czystości produktów. Ta metoda jest szczególnie przydatna w przypadku mieszanin zbliżonych pod względem temperatur wrzenia. Innym rodzajem jest destylacja azeotropowa, która stosowana jest w sytuacjach, gdy składniki tworzą azeotrop – mieszaninę o stałym składzie i temperaturze wrzenia. W takich przypadkach konieczne może być dodanie substancji trzeciej, aby umożliwić separację składników.
Jakie są najważniejsze urządzenia do destylacji rozpuszczalników
Aby przeprowadzić proces destylacji rozpuszczalników skutecznie i efektywnie, niezbędne są odpowiednie urządzenia i sprzęt laboratoryjny lub przemysłowy. Podstawowym elementem wyposażenia jest aparat destylacyjny, który składa się z naczynia do podgrzewania mieszanki oraz układu chłodzącego do kondensacji pary. W laboratoriach często stosuje się prosty aparat destylacyjny składający się z kolby okrągłodennej oraz chłodnicy Liebiga. W przemyśle natomiast wykorzystuje się bardziej zaawansowane systemy destylacyjne, takie jak kolumny frakcyjne wyposażone w różnego rodzaju packingi lub talerze, które zwiększają powierzchnię kontaktu między parą a cieczą. Dodatkowo ważnym elementem jest termometr służący do monitorowania temperatury wrzenia poszczególnych składników oraz manometr kontrolujący ciśnienie wewnętrzne układu. W przypadku bardziej skomplikowanych procesów mogą być także wykorzystywane automatyczne systemy sterowania oraz monitoring procesów technologicznych.
Jakie są kluczowe czynniki wpływające na skuteczność destylacji rozpuszczalników
Skuteczność procesu destylacji rozpuszczalników zależy od wielu czynników, które należy wziąć pod uwagę podczas projektowania i przeprowadzania tego procesu. Jednym z najważniejszych aspektów jest różnica temperatur wrzenia składników mieszaniny. Im większa różnica, tym łatwiejsze jest oddzielenie substancji. W przypadku składników o zbliżonych temperaturach wrzenia konieczne może być zastosowanie bardziej zaawansowanych metod, takich jak destylacja frakcyjna. Kolejnym istotnym czynnikiem jest ciśnienie atmosferyczne, które wpływa na temperatury wrzenia substancji. W obniżonym ciśnieniu temperatura wrzenia składników również maleje, co może być korzystne w przypadku substancji wrażliwych na wysokie temperatury. Również szybkość podgrzewania ma znaczenie; zbyt szybkie podgrzewanie może prowadzić do niepożądanych reakcji chemicznych lub nieefektywnego oddzielania składników. Oprócz tego, jakość używanych materiałów oraz ich czystość mają kluczowe znaczenie dla uzyskania wysokiej jakości produktów końcowych.
Jakie są wyzwania związane z destylacją rozpuszczalników
Destylacja rozpuszczalników, mimo swoich licznych zalet, wiąże się także z wieloma wyzwaniami, które mogą wpłynąć na jej efektywność i bezpieczeństwo. Jednym z głównych problemów jest ryzyko powstawania azeotropów, które utrudniają separację składników o podobnych temperaturach wrzenia. W takich przypadkach konieczne jest stosowanie dodatkowych substancji lub zmiana warunków procesu, co może zwiększać koszty i czas produkcji. Innym wyzwaniem jest kontrola temperatury oraz ciśnienia w aparacie destylacyjnym; niewłaściwe ustawienia mogą prowadzić do nieefektywnego oddzielania składników lub nawet do uszkodzenia sprzętu. Dodatkowo, wiele rozpuszczalników jest łatwopalnych lub toksycznych, co stawia wysokie wymagania dotyczące bezpieczeństwa pracy oraz ochrony środowiska. Niezbędne są odpowiednie procedury zabezpieczające oraz systemy wentylacyjne w pomieszczeniach, gdzie prowadzony jest proces destylacji.
Jakie są różnice między destylacją a innymi metodami separacji
Destylacja rozpuszczalników to jedna z wielu metod separacji składników mieszanin, jednak różni się ona od innych technik zarówno zasadą działania, jak i zastosowaniem. Na przykład, ekstrakcja to proces polegający na wykorzystaniu rozpuszczalnika do wydobycia pożądanych substancji z materiału stałego lub cieczy. W przeciwieństwie do destylacji, ekstrakcja nie opiera się na różnicy temperatur wrzenia, lecz na różnicach w rozpuszczalności składników. Inną popularną metodą separacji jest filtracja, która polega na oddzieleniu ciał stałych od cieczy za pomocą porowatego materiału filtracyjnego. Filtracja jest skuteczna tylko w przypadku mieszanin zawierających stałe cząstki i nie nadaje się do separacji cieczy o podobnych właściwościach fizykochemicznych. Z kolei chromatografia to technika separacyjna oparta na różnicach w powinowactwie składników do fazy stacjonarnej i ruchomej; jest ona często wykorzystywana do analizy skomplikowanych mieszanin chemicznych oraz oczyszczania substancji aktywnych.
Jakie są przyszłe kierunki rozwoju technologii destylacji rozpuszczalników
W miarę postępu technologicznego i rosnących wymagań dotyczących efektywności procesów przemysłowych, technologia destylacji rozpuszczalników ewoluuje w kierunku bardziej zaawansowanych i ekologicznych rozwiązań. Jednym z obiecujących kierunków jest rozwój metod destylacji opartej na wykorzystaniu energii odnawialnej, takich jak energia słoneczna czy geotermalna. Dzięki temu możliwe będzie zmniejszenie kosztów operacyjnych oraz ograniczenie emisji gazów cieplarnianych związanych z tradycyjnymi źródłami energii. Ponadto, coraz większą uwagę przykłada się do automatyzacji procesów destylacyjnych poprzez zastosowanie nowoczesnych systemów monitorowania i sterowania, które pozwalają na optymalizację parametrów pracy urządzeń oraz zwiększenie ich wydajności. W kontekście ochrony środowiska rozwijane są także technologie odzysku cennych surowców z odpadów przemysłowych przy użyciu innowacyjnych metod separacji chemicznej. Również badania nad nowymi materiałami dla kolumn destylacyjnych mogą przyczynić się do poprawy efektywności procesów separacyjnych poprzez zwiększenie powierzchni kontaktu pary z cieczą oraz redukcję strat energetycznych.
Jakie są kluczowe aspekty bezpieczeństwa podczas destylacji rozpuszczalników
Bezpieczeństwo podczas procesu destylacji rozpuszczalników jest niezwykle istotne ze względu na potencjalne zagrożenia związane z używanymi substancjami chemicznymi oraz warunkami pracy. Przede wszystkim należy zapewnić odpowiednią wentylację pomieszczeń laboratoryjnych lub przemysłowych, aby uniknąć gromadzenia się oparów łatwopalnych lub toksycznych substancji. Używanie sprzętu ochronnego takiego jak rękawice, okulary ochronne czy maski jest obowiązkowe dla pracowników zajmujących się obsługą aparatów destylacyjnych. Ważne jest również regularne przeprowadzanie przeglądów technicznych urządzeń oraz kontrola ich stanu technicznego; wszelkie usterki powinny być natychmiast usuwane przez wykwalifikowany personel. Dodatkowo warto wdrożyć procedury awaryjne na wypadek wystąpienia niebezpiecznych sytuacji takich jak pożar czy wyciek substancji chemicznych; pracownicy powinni być przeszkoleni w zakresie reagowania na takie incydenty.
Jakie są najczęściej stosowane rodzaje rozpuszczalników w procesach destylacyjnych
W procesach destylacyjnych wykorzystywane są różnorodne rodzaje rozpuszczalników, które dobierane są w zależności od charakterystyki przetwarzanej mieszaniny oraz celów technologicznych. Najczęściej stosowanym rozpuszczalnikiem jest etanol, który dzięki swoim właściwościom chemicznym znajduje zastosowanie zarówno w przemyśle spożywczym jak i farmaceutycznym. Inne popularne rozpuszczalniki to aceton oraz metanol; oba te związki charakteryzują się niskimi temperaturami wrzenia i dużą zdolnością do rozpuszczania różnych substancji organicznych. W przypadku procesów przemysłowych często wykorzystywane są także bardziej specjalistyczne rozpuszczalniki takie jak dichlorometan czy heksan; te związki mają swoje specyficzne zastosowania w ekstrakcji czy oczyszczaniu substancji chemicznych. Ważne jest jednak pamiętać o bezpieczeństwie przy pracy z tymi substancjami; wiele z nich ma działanie toksyczne lub łatwopalne, co wymaga zachowania szczególnej ostrożności podczas ich używania i przechowywania.